「現場改善コンサルティング事業」の導入事例2例をご紹介いたします。お客様から依頼を受けた課題に対し、実際の現場をしっかり調査・分析し、最適なプランを提案。それに基づき、お客様と共に現場改善施策を導入し、数値化できる確かな成果を生み出しています。
A社は、光学機器を中心とした自社製品製造と受託生産を行っているメーカー。クライアントの主力製品が海外生産にシフトされたため、国内事業所の生産高が半分以上落ち込み、受託生産事業の拡大を目指し、平山にコンサルティングを依頼。
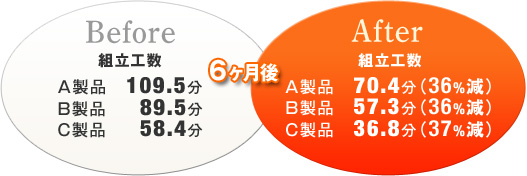
-
- 現場改善の知識と経験不足により、工数削減が推進できない
- 工数削減に取り組むためのシステムが構築されていない
- ムダ削減への具体的な目標が定まっていない
-
- 現状のラインレイアウトでは、組立工数削減につながりにくい
- 作業台と部品の配置が悪く、組立作業者の動作が多すぎる
- 部品供給BOXが、作業の効率性を考慮していない
-
- 半期改善目標の立案・設定
- コンサルタントによる現状分析・問題点摘出・改善実施・成果確認を毎月実施
- 管理監督者による自主改善を、毎日実施
- ラインレイアウトの変更
- 作業台・部品・治具・工具の配置改良、作業員の動作を軽減、作業手順を見直す
-
- 半期改善目標を達成
- 現場改善に取り組むPDCAが回り出した
- 現場の小さなムダも見逃さない“ムダ取り”が出来る人材に成長
- 新規受託製品受注時の早期立ち上げが可能に
「トヨタ生産方式」の導入と、 改善を継続推進できる「人材育成」も 同時に実施できることが決め手に。
- 「トヨタ生産方式」を基本にしている
- 座学ではなく現場での改善実践を掲げている
- 改善を継続推進できる「人材を育てる」ことを目的にしている
改革の方向性が当社と合致していたことも大きな決め手になりました。
B社は、成形、焼成、仕上げ工程を持つ自社製品製造メーカー。1工場で60万個/月の生産能力があるにも関わらず、現状は40万個/月の生産のみで、残りの20万個/月を別工場で生産。1工場の本来の能力のフル活用を、平山と共に目指した。
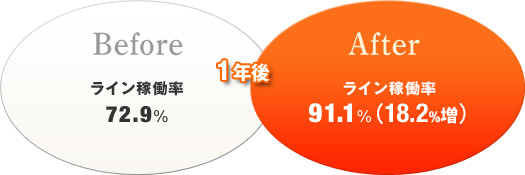
-
- ライン停止の多発が、設備稼働や生産量に影響を与えている
- 「予定生産数に達成しなくてもいい」といった風潮の蔓延
- 技能員たちの生産に対する意識レベルが低い
-
- 設備部位別にライン停止の原因調査を実施
- 設備の予備品管理体系ができていない
- 改善状況、製造工程の見える化が徹底されていない
- 性能試験のリードタイムが長い
-
- ライン停止原因を重点に改善を実施 ( 離形剤塗布方法の見直し等)
- 予備品管理の実施により保守部品の欠品を撲滅
- 改善状況と工程進捗を見える化し、問題点の共有化を図る
- 性能試験を内製化し、検査と試験を同時に実施
-
- ライン稼働率向上により、1工場で生産目標を達成
- 保守部品欠品によるライン停止時間を削減
- 技能員の生産量、ライン停止に対する意識の向上
- 計画通りの生産を実現し、お客様視点の活動が可能に
徹底的な実態把握と、平山と当社の改善活動の視点が合致していたことが、一番の理由でした。
- 顧客視点の活動
- 標準作業をベースとした生産づくり
- 工場をショールーム化した全体最適の追求
- すべての工程を見える化する管理システムの構築
- 改善を介した人材育成
など、当社と改善活動の視点が合致していたこと。
さらに、コンサルティング依頼後、現場調査に3日間費やし、当社の実態を正確に把握する姿勢が気に入りました。